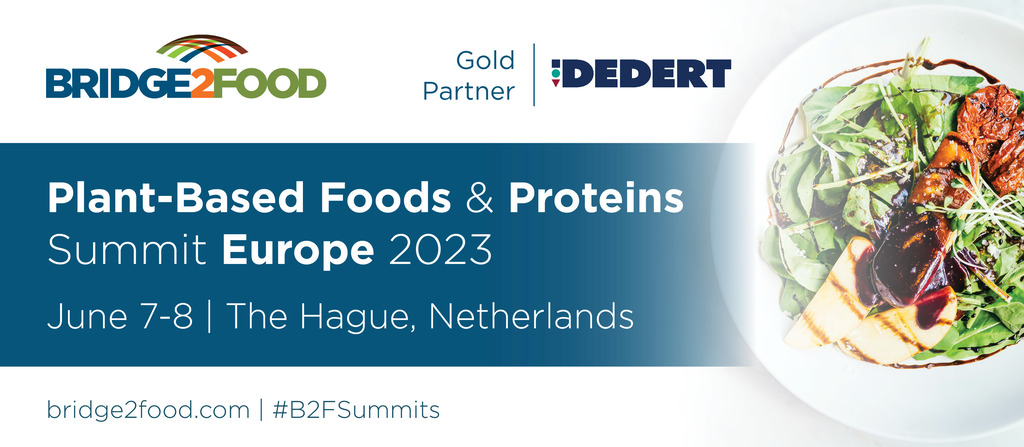
Q&A: Sustainability a key focus for process technology innovations with Dedert
Sustainability is a cornerstone in the shift to alternative proteins and plant-based ingredients. Dedert Corporation understands how sustainable design and process customization are connected. Join market manager Gregory See Hoye at the Plant-Based Foods & Proteins Summit Europe, June 7 at The Hague, to talk about process innovations in drying and evaporation. In advance of his presentation, he answers a few questions.
How do alternate drying technologies, such as Dedert’s ring-drying system, reduce production costs?
The concept of improving production costs by improving energy-efficiency and sustainability-features of the process system is not necessarily a function of just the drying system or any other unit operation. Rather, it’s about understanding how the integrated process works together and the impact on the product or application. For example, when developing the manufacturing process for a plant-based or fermentation protein, spray drying is often selected due to commonality and easy accessibility at the smaller demonstration-scale. Spray drying is very suitable for liquid feeds requiring water-removal into a dry powder. Some proteins behave ideally with spray drying and should continue to be processed in this way. However, many proteins exhibit potential to be further dewatered prior to final drying, which would reduce the thermal load required for final processing and therefore improve the overall plant operations and energy costs. Ring drying is a suitable technology to evaporate water from a paste or slurry (effectively a wet solid) to produce a final dry powder, but has to be combined with an appropriate upstream process comprised of mechanical dewatering and other modifications for food/product safety, e.g. pasteurization. In the case where spray drying remains more appropriate, then optimizations around more efficient or maintenance-free atomization technologies, such as Dedert’s Air Bearing Atomizer (ABATM), may offer operational benefits.
Does Dedert have new drying technology that will benefit the alternative-protein industry?
Dedert customizes technologies to meet changing market requirements. Currently, we are working on the ring dryer concept specifically for plant-based proteins as well as several spray dryer technologies for fines control or energy-efficiency, plus technology integration for heat-recovery and water-recovery opportunities. The alternative protein industry remains in a state of evolution and growth, so many development opportunities remain to be explored, including valorisation of co-products and corresponding processing requirements. Dedert partners with innovative groups to evaluate these opportunities towards finding efficient solutions that meet specific and changing expectations.
What can be done with evaporators to improve a company’s environmental impact?
Evaporators are a simple operation to recover additional value from a nutrient-rich wastewater stream. In some instances, value exists to install an evaporator upstream of a spray dryer (or ring dryer) to help reduce the thermal load on the dryer, which in turn lowers energy consumption and environmental footprint. Evaporators offer the possibility to collect condensed steam as a source of additional heat (e.g. heat recovery) and combined with polishing steps may offer a source of recycled process water to help reduce water consumption. Alternatively, gas-heated evaporators may be driven on dryer exhaust gases as a source of heat recovery through system integration opportunities.
What other opportunities are there for process water recovery?
Many 3rd-party technologies exist and can be explored for water recovery, including packages that condense/recover water from dryer exhaust gases, but cost/benefit considerations need to be evaluated on a case-by-case basis. Depending on the product applications, Dedert can also explore concepts around closed-loop or partially closed-loop drying, for example, which recover heat and improve energy-efficiency, but also provide a source of steam-rich hot air which can further condensed for heat and water recovery. Discussions around specific applications are needed to establish a fit for these specialty technologies.
What role does collaboration play in developing sustainable technology innovations?
As the alternative protein industry remains in a state of evolution and growth, new opportunities continue to develop as initiatives to improve product quality, functionality, and manufacturing processes for sustainability/efficiency. Collaborations are critical in the development of the corresponding solutions, combining the expertise of companies focused on best available technologies in their specific fields. Through these collaborations, integrated process systems can be developed to ensure that the most optimized solution is implemented to meet the sustainability goals and values of the manufacturer. Innovations include the integration of ring drying for protein applications, optimized spray drying atomization, possibilities for dry functionalization or pasteurization, and other heat-recovery or water-recovery technologies.
What do you foresee for the near future in processing innovations?
As the industry continues to evolve, manufacturers will continue to shift their focus towards their product development challenges, leaving processing and related innovations to the equipment suppliers. However, equipment suppliers are generally not equipped to fully develop complete manufacturing processes so a reliance on partnerships with process consultants and specialized innovation centers will become more important to identify the relevant innovations. Joint initiatives between these three (3) groups will play an important part through the development of specialized Pilot Plants or demonstration facilities to establish best practices and optimized technologies based on particular applications and expectations.
Join Greg at Summit Europe June 7-8 for what will be an informative presentation “Sustainable Processing Innovations Welcome.” Find more details and register here.